This is for my cousins or friends who don’t do their own oil changes.
Here is a home project you can do that doesn’t take much time or money. If you call a plumber you’re looking at maybe $75. If you DON’T do this periodically you will have higher water bills from future leaks.
A couple of weeks ago I noticed that the handles in the master bath shower were turning PAST the shut off position I had set them to the last time I replaced the washers. That was in January of 2004. This means that the washers are wearing and requiring more turn to shut off the water. Time to replace. No problem. I’ve done this a few times before. I knew that I would need:
A flat head screwdriver
A Phillips screwdriver
A rubber “strap wrench (Nice to have around the house…$5 maybe??)
An adjustable wrench or set of open end wrenches
A faucet handle puller (approx $10…and I already had one)
An “assortment pack” of replacement washers. (about $2)
I could not find my faucet handle puller tool and chalked it up to it being appropriated by the jerk who I let live at my house for a couple of months. He was a home handyman as his profession. When he moved out I’ll bet he “needed” those tools and was upset at me for kicking him out. Oh well, I won’t lose the replacement. It will be stored under the bathroom sink, where I will need it in the future.
So, here we go. Put some form of cover over the drain. You don’t want to drop a screw and lose it down the drain.
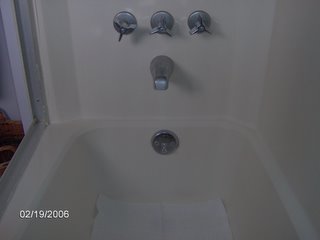
Now, go to your main shutoff for the water entering the house. Turn it off. Go back to your valve and open it. In my case my valve is the cold water side of the shower. “Open it” means turn it on as if you intend to take a cold shower. There shouldn’t be any water flow because you shut off the main first. Now, go to another faucet, preferable LOWER in your house, and open that for a few seconds, then close it. This will let off some pressure in the water line.
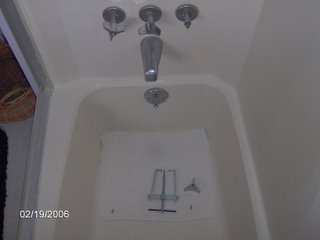
Go back to your valve. If the valve isn't open at this time, open it...more on this later. Remove the screw from the handle and use the handle puller to remove the handle (in my case I am really going to do BOTH hot and cold, so you see an extra screw in the picture.
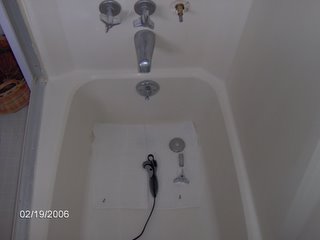
Using a strap wrench, remove the step trim tube and escutcheon plate. You use a tool like this because you don’t want to mar the finish on these pieces. In the past I have wrapped duct tape around jawed pliers, but then you have to take tape off and gum up your pliers. Trust me, a strap wrench is cheap and a better way.

Using a CORRECTLY sized open end wrench or adjustable wrench, engage the 2 flat spots on the valve stem and remove it (Ladies: Counter clockwise. Men: You don’t need directions).
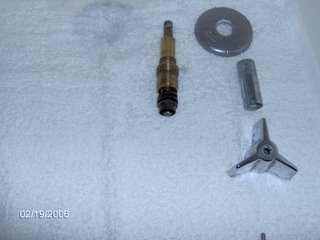
You are looking at the “business end” of the removed stem. A small screw retains the black washer which needs replacing. Remove the screw and pull out the washer. Yeah, your fingers are going to get a little black, but it washes of later.
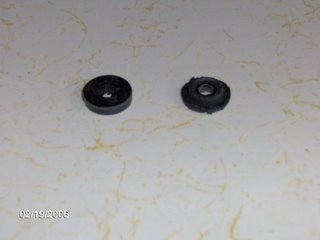
NEW washer on the left and old worn washer on the right. Go to your assortment pack and choose a replacement washer that fits the back end of the stem. Compare that to the washer you removed and you will easily see washers that DON’T fit and which one does fit. Put the washer in place and replace the screw. Do not over tighten the scew so it deforms the new washer. Just snug the screw up to it and give another little “skosh” of a turn.
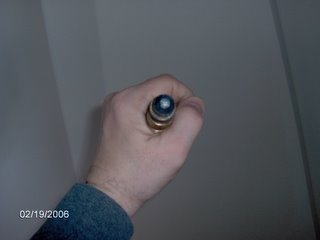
That’s what the back end of the stem looks like with the new washer in place.
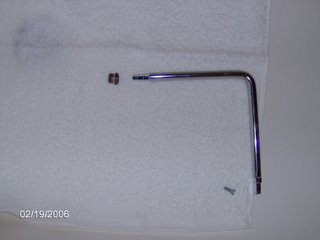
This is the part my dad likes…where I admit a mistake. WHAT IS that little piece and tool??
When I pulled out the stem another piece, called the “valve seat” came out with it, due to the friction between the washer and the valve seat. This is why I said above (before removing the handle) to open the valve. I didn’t, and the valve seat came out with it. Simple, though. This special tool is like a big Allen Wrench and allows you to remove or replace valve seats. Costs about $6. I didn’t mind the extra cost.
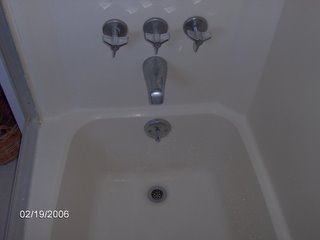
Reinstall the valve stem and snug it up tight. Loosely put the handle on, no screw, and shut off the valve. Then align the handle the way you want it to look when shut off and replace the screw. My handles all point straight down when they are shut off. If they start to look different in the future, it is time to replace the washers again. In my case, that is about every 2 years. Next time the outlay will only be about a dollar for a pack of the correct sized washers. 10 come in a pack. That’s enough to change the washers every 2 years 5 more times (10 years)…for $1. Ka-ching!! Don’t hire a plumber…this is pretty easy.
Finally, go back and turn on your main water to the house. Then go to each sink and shower and open the valves to allow any air to escape. They will "spit" a little air...don't be alarmed. Just open for a few seconds until the spitting stops then close. Do this for all your sinks and showers.
That's it!!
Oh yes, I keep a spreadsheet of common household repairs. I repeated the entry for replacing the master bath shower washers...Feb 2006. Nice little reference to have.