Last night, as I was putting together pieces for my air compressor plumbing, that song came on the radio. It didn't occur to me until today how appropriate that was. After all I was plumbing for air (wind) that would be used to blow around sawdust. And now I am reminded of how Bill and Ted demonstrated "All we are is dust in the wind" to Socrates during their Excellent Adventure.
OK, I digress.
Today, during lunch, I got to go home and do some more work on this project. All of the horizontal main line parts were cut to correct length, cleaned, and dry fitted. The hard part was getting the lengths right so that things line up with wall studs. The "6 foot between drops" idea was modified so that drops would be adjacent to studs, which are 16 inches on center. So 6', 12', and 18' became 5'4", 12', and 17'4". Close enough.
This morning before going to work I measured where the drop to the outside would go. According to my plan, it was going to end up too high off the ground for my taste. So I am going to install that part BETWEEN the two valves instead of ABOVE both of them. But, also, the part that would poke through the wall was made too short. So I need to simply make a new one. Piece of cake now.
Also, I went by a "tool fittings" supplier and ordered the quick connects and had them make up a 3 foot hose to connect the compressor to the system. The parts will be in tomorrow and I can get them during lunch. Looks like I will be finished on Friday night or Saturday.
Tonight I sweated all the joints I prepped in the afternoon, mounted the horizontal run, and built the vertical run to the compressor.
I marked the studs, then temporarily installed some finish nails in the studs to hold up the horizontal run.
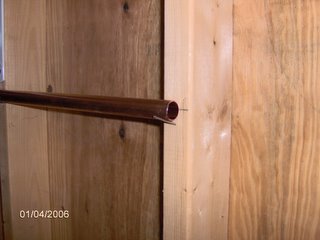
Then, I soldered up all the parts of that horizontal run.
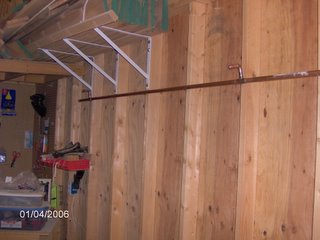
One by one I replaced the finish nails with pipe straps to secure to the wall.
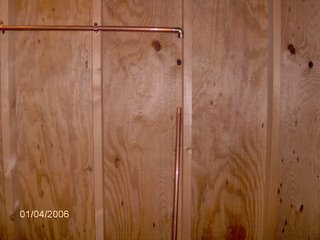
Then built the vertical run. This shows the shutoff to the compressor, which I ran to the right. Below that is the new and improved drop that will go outside. That long leg is just dry fitted for now. Below that is the ball valve for the drain.
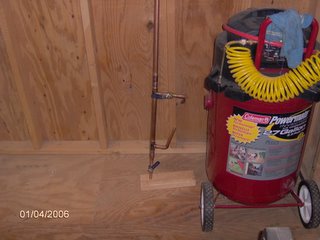
So, just a few simple things left.
1. Pick up the quick connectors tomorrow at lunch.
2. Solder the vertical parts to the elbow above it.
3. Drill a hole in the wall for the outside drop.
4. Put the stub into the hole and solder that.
5. Tighten up all the strap screws.
6. Conceal everything with all the junk I keep in my shop.