OK, pictures will tell the story better, but I will add text just in case. The text for a picture will be above the picture.
This is a picture of a barrel stave before the curve is cut. It is a trapezoid and is 8 inches long. The pencil line is on the "inside" of the stave at exactly the halfway point, and is used to align the stave for cutting the curve.
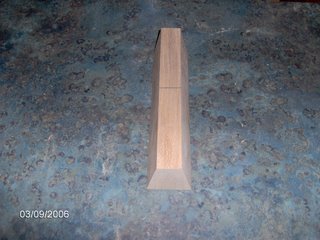
13 of those staves when placed together form a circle. Here is one view with only 5 staves.
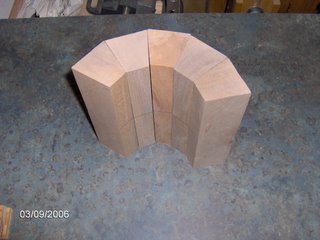
And here is another view.
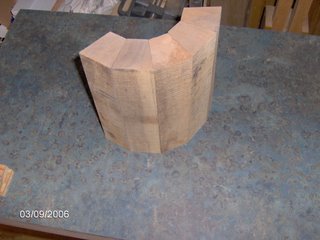
To cut the curves accurately I needed a circle cutting jig. This consists of a table and a swing arm.
Here is a picture of the table, attached to the bandsaw. For these pictures I have set a metal ruler on it. The table is 4 feet long and supported by the metal table of the bandsaw and a support leg on the opposite end.
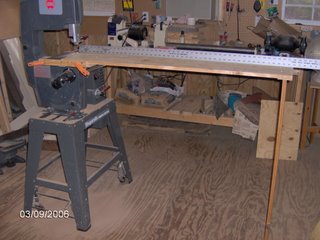
Looking at the top of the table, I have drawn a center line down the entire length. This is in perfect alignment with the teeth on the bandsaw blade. On this line I have marked and drilled holes at 11.75 inches (for an 8 inch barrel)...
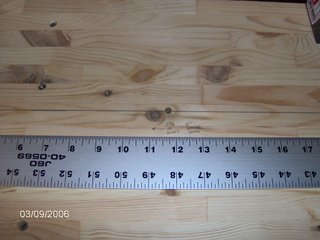
...and 45 and 5/8ths inches (for a 20 inch barrel), which I LATER found was a mistake!! The hole is supposed to be at 47 inches. So I simply drilled another hole, which is the BEAUTY of this system. Wherever I need a new center point, measure, mark, and drill a new hole.
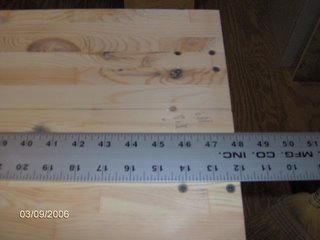
The other part to this system is a "swing arm", which is made up of 2 parts. The first is simply a long piece of wood, marked with a center line just like the table. The other part is short and is a "carrier" for the stave. They are simply screwed together. This picture shows both parts...

...and this picture is looking down the length.
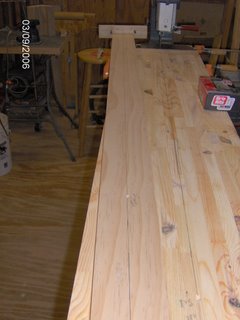
Holes are drilled in the swing arm, just like in the table, on the center line. The swing arm is placed on the table and the two holes are fixed together with a 1/4 inch dowel. The dowel allows the swing arm to, well, swing. In this picture I set a screwdriver on top pointing to the dowel. Sorry it's out of focus.
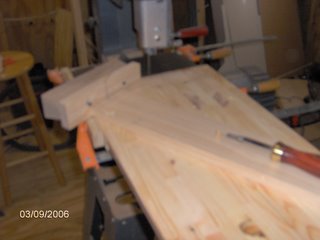
To cut a stave it needs to be mounted onto the carrier part of the swing arm. Marks are made for alignment and it is held with short screws.
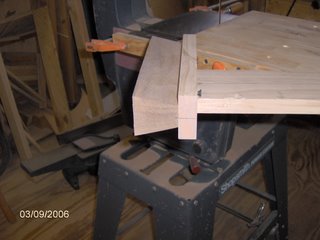
After cutting the stave is removed from the carrier and the waste part (left in the picture) can be discarded (a little blurry).
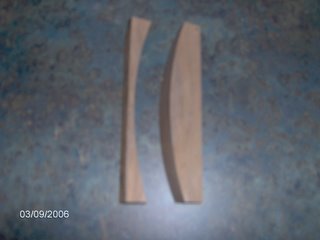
This picture (blurry) shows the stave just cut in relation to the other staves.
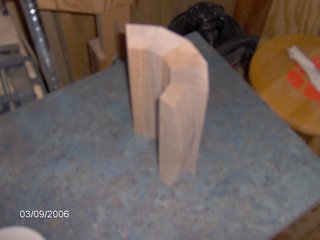
Finally, when the process is repeated for all 13 staves, and those are fastened together, it starts to really look like a barrel.
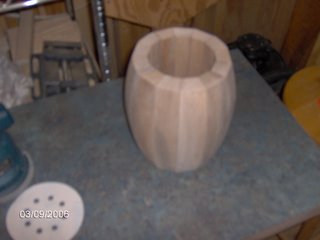
At this point the barrel needs some sanding but I'm not going to make it a beautiful polished work of art. Maybe 120 grit max. Then some stain...no finish. It should look a little weathered and worn to be authentic.
Now I need to make a permanent bottom and a removeable lid. Then I will take some black strap material and surround it to look like barrel hoops.
N'est-ce pas?