Treebeau
Wednesday, May 31, 2006
Wednesday, May 24, 2006
Anatomy of a pen
For anyone who is curious about how pens are made.
Starting with a block of wood, cut it into two rectangular pieces that are about 3/4 x 3/4 by 2+1/4 inches. Then drill a 7mm hole down the length in the approximate center. Rough up the brass tube inserts with sandpaper, apply glue, and slide them into the holes. Let cure overnight. Mount the two blocks together on a "mandrel" on the lathe, turn the the desired profile, sand very smooth, and apply stain/finish.
Press the pen tip into one "barrel" and the clip/cap into the other barrel. Press the brass end of the twist mechanism into the other end of the barrel that has the tip (not too far at first...will be fine tuned). Screw in the pen refill. Twist to "open" to check how far the refill comes from the pen tip. If a little more is desired, remove the refill and press the twist mechanism in a little more. It cannot be backed out, so care must be taken. Finally, slide the trim ring over the twist mechanism then the bottom barrel. Done.
Here is a picture showing the relative order (top to bottom) of how it is done, and the relative positions (left to right) of the pen parts.
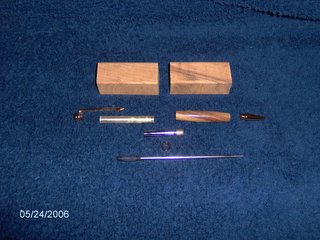
The next picture is a sort of "before and after". I am always amazed at how pretty just about any block of wood is when it is machined. A fairly attractive yet rough piece of wood like this red keiyaki comes out beautiful. If you look really closely at the right end of the finished piece you can see that a little chip came off and exposed the brass tube. The piece is ruined but I still finished it to see how nicely it sands and takes stain and finish. I like the look of this wood very much and have enough blanks to make 3 more pens from it.

Monday, May 22, 2006
Blue Keiyaki (Zelkova) and Teak pens
The first two pictures are the front and back of a pen made from blue keiyaki, also known as "zelkova". The wood was sent to me by a woodworking friend in Tokyo.
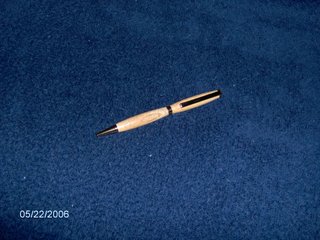
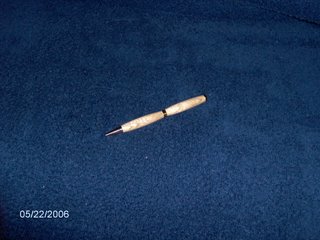
The next two pictures are side views of 2 pens made from teak. The wood was salvaged from a boat restoration project being done by a woodworker in coastal NC.
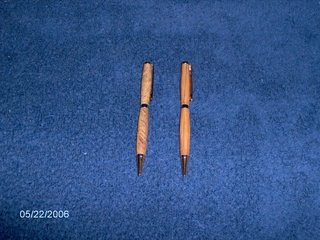
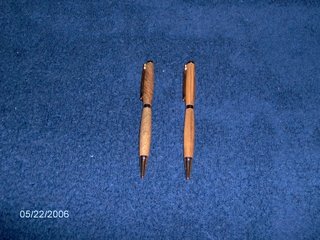
Sunday, May 21, 2006
Cyclone, sycamore, teak and "blue keiyaki"
I took a break from working on the chess set and did some other shop stuff.
When I got my tax return I purchased a cyclone dust collector which is the best thing a woodworker can do to aid in cleanup and to keep the lungs clear of fine sawdust. The machine came in 3 boxes and required some assembly. I found that there was a crack in the upper part of the cyclone and contacted the manufacturer, who will be sending a replacement. In the meantime I did some assembly and need to make some brackets to hang the unit before I can continue.
http://www.clearvuecyclones.com
A friend of mine needed help taking recyclables to the landfill and disposing of an old computer. One of the things she was throwing away was a "dry erase white board". It looked to me like the aluminum frame was falling apart. Her 11 year old daughter seemed to be a little upset that this was being thrown away...probably had lots of fun drawing on it. Without her knowing I kept the white board and discarded the aluminum frame. Then cut the white board down into two smaller pieces to remove some edge damage. Then I made a frame for one of the pieces out of some sycamore... the same sycamore that came from her yard (and was used to make the gift coffee barrel for her). The frame needs some finishing touches, sanding and staining. I think the daughter will be surprised at having the board back and with a frame that came from her own tree. If they like it I'll do the same for the other small piece of white board.
And today I turned some pens. Two out of teak and one out of "blue keiyaki". A couple of interesting stories. The teak comes from a woodworker who lives in coastal NC. He is refinishing an old boat. I believe that some deck boards had to be replaced. Whatever was salvageable was cut into "blanks" for making pens and he sent them to whoever asked for them. I asked for two and he sent me 10. FREE !
The blue keiyaki comes from downtown Tokyo. Another woodworker acquaintance lives there and owns a liquor and cigar store. In his spare time he does (excellent) woodworking. He stumbled across a house in downtown tokyo that was being cleared. Along with that were some old trees which were going to be dumped. He put in a lot of sweat equity and harvested everything he could (for free) from those trees. Then he cut pen blanks and offered them to whoever asked...all he wanted was to recover shipping costs. He sent me a few blanks each of "blue keiyaki", "red keiyaki", and "sakura".
A month ago I tried to do a microwave drying of 1 of each variety, and accidentally destroyed one of the pieces of sakura (it's a cherry tree variety). Along with what I turned today I tried a blank of the Red Keiyaki. It was looking REALLY NICE, but then a bit of rot showed up and the wood basically blew apart on the lathe. One half of the pen was almost intact, so for fun I went through the sanding and finishing stages to see what it would eventually look like. It should make gorgeous pens.
Pics later.
Thursday, May 18, 2006
Cherry team done.
Here are the cherry knights. Yes, they look different from each other. Every time I make a piece it looks different. Yet they look like they are on the same team, and that is what is important to me. A chess set of two teams, yet no two pieces look exactly alike.
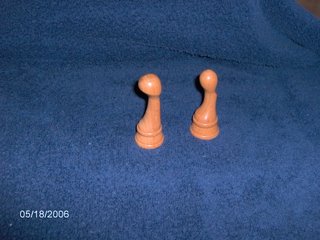
And here is the cherry team.
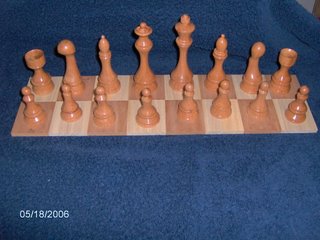
When the poplar team is done I need to drill holes in the bases fill with shot, plug, and add felt. I've already experimented with a scrap piece and it adds a nice bottom weighting...not as easy to tip over.
Decided that I will build the chess board as a moveable box, rather than a table with drawers. The gift recipient would like it to be portable.
Monday, May 08, 2006
First Knight
Before getting to the knights, I first finished the rest of the pieces, with the completion of the Cherry Queen.
Here are all the pieces except the knights.
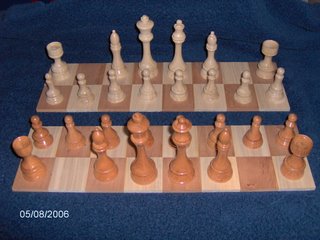
Then using some scrap I made a "practice" knight. This requires an "offset turning" technique which I have never tried before. It turned out ok, but I made some mistakes. I will make 1 more practice piece without applying finish to get the "kinks" out. Remember, this is LATHE work, not a carving, so it is a "stylized" piece...not a horse. Just think of how Picasso might have drawn a horse. The curve of the "neck" comes from the offset turning.
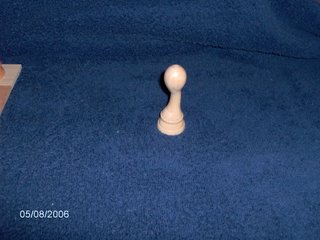
And finally, one of EACH style of piece.
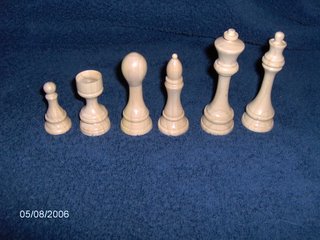
Saturday, May 06, 2006
The Royal Treatment...several pictures
I had time today to make a king and document it with photos. So, in case anyone wants to see how I have done each chess piece...here goes:
(Click on any picture to maximize it)
First I start out with some wood. I cut it to 1.5 inches wide and plane one face of each piece, then glue the planed faces of two pieces to make a block. The length of the block is the length of a desired piece plus 1.5 inches waste.
Here are the future cherry king and queen:
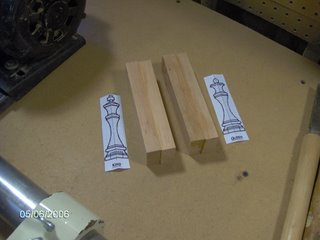
I use the pattern to set a caliper to the largest diameter of the piece to be turned.
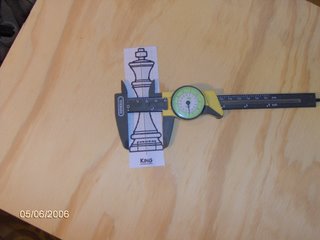
Then the block gets chucked into the lathe and turned round down to that largest diameter.
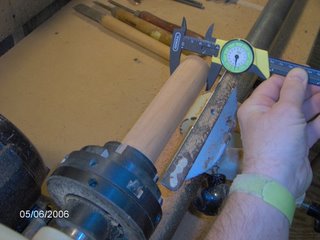
The pattern is folded in half and placed against the cylinder. I mark key points on the cylinder with a pencil.
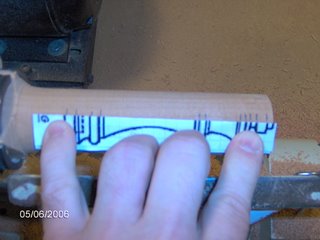
Then each pencil mark is extended completely around the cylinder by holding the pencil on a mark and turning on the lathe.
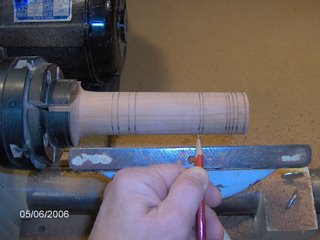
Using a parting tool and caliper I turn down the cylinder to final diameter at each of the key points.
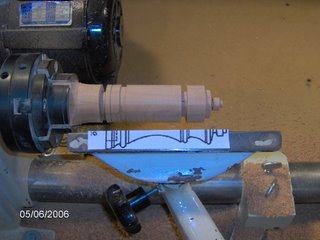
Then with other tools I make the final shape of the head of the piece.
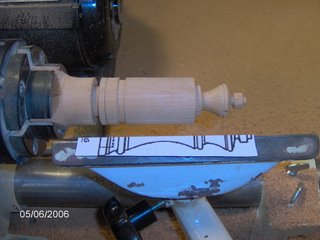
And then the bottom and start scooping out the middle.
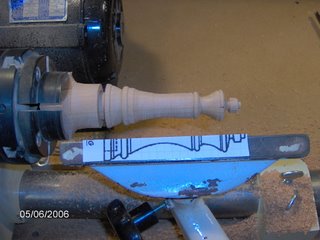
And this is what it looks like when all the shaping is done.
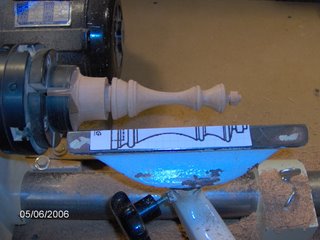
Then I sand down to 400 grit, apply 0000 steel wool and hold wood chips against the turning wood to "burnish" it. It begins to shine without any polish.
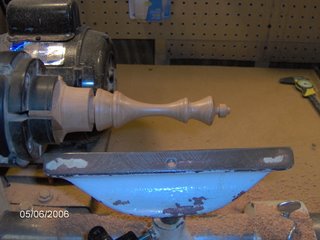
THEN I apply the polish. The polish has a slight tint and some grit in it which polishes it to something like 1200 grit. It looks wonderful after that. Takes on the final dark look and very shiny and smooth.

But to protect it I go a little farther and add a coat of Shellawax, which is a durable finish and makes it shine even more.
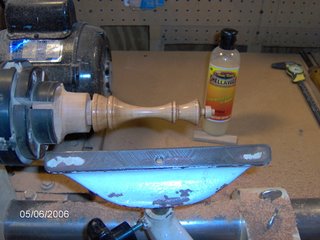
And then I use a parting tool to turn it off the waste base. This leaves a small nub which I pare away with a chisel. Then I flat sand the bottom a little and have a piece that is ready to play.
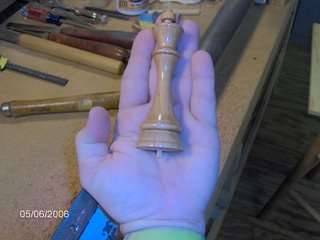
There are a few more steps to do.
1. Each piece will have a hole drilled into the bottom. 1/2 inch diameter, 3/4 inches deep.
2. 1/2 inch of the hole will be filled with shot, then a 1/4 inch plug will be glued in. That gives the piece more weight at the base.
3. Each piece will get felt glued on the base.
I bought a box of 10 shotgun shells and spent about an hour opening them and removing all the shot. What I didn't know is that there is a white substance that resembles salt all among the shot in the shell. So, similar to separating an egg white from the yolk I poured shot between Dixie cups to remove the "salt" or whatever it is. It would be nice if I now have enough shot, but I don't know how much I need, which is enough to fill 32 holes that are 1/2 inch deep and 1/2 inch diameter.
Thursday, May 04, 2006
Mini update
Chess set:
All the 8 cherry pawns are done as well as both rooks and 1 bishop. Remaining are the other bishop, the king, the queen, and all 4 knights.
Tae Kwon Do:
Last Saturday I did my second of 7 maintenance tests to earn my third degree black belt. Will be another 2 years or so of training to get there.
Work:
SO busy. Meetings EVERY day several times each day. So tiring that I don't have desire to go out to the shop and do fun stuff.
Outdoors:
Last weekend JP and I put in 6 solar powered walkway lights.
The Weekend Ahead:
I want to turn out the cherry bishop, at least. Going for pizza and a ball game on Saturday night. Need to make a couple of minor changes to the bamboo fountain. Maybe buy and put in 4 more solar walkway lights. Oh yes, I rented the movie "Walk the Line" to watch.